Work coordination platform
Designed for the automotive industry
As a leader in innovation, you understand the importance of staying ahead of the curve in the fast-moving automotive 4.0 world. KanBo provides you with the tools to do just that by facilitating smart factory operations, streamlining project management, fostering collaboration and solving complex problems.
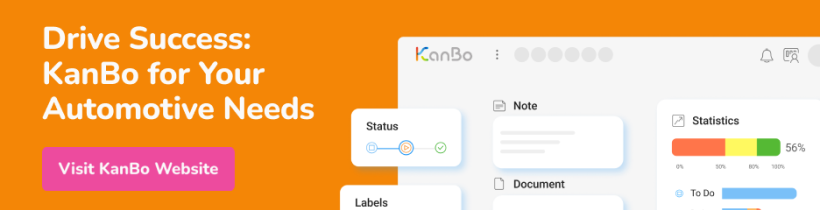
Efficient Time Management and Maintenance Associate: The Indispensable Role of KanBo’s Timeline View in Automotive Projects
In today’s fast-moving automotive industry, efficient time management is key to staying ahead of the competition. That’s where KanBo, a work coordination platform designed for large enterprises, comes in. Its Timeline view feature is an indispensable tool for ensuring projects are completed on time and within budget.
With Timeline view, teams can visualize a project’s progress and dependencies in a single view, making it easier to plan and manage their workloads. This is especially helpful for teams working on complex projects with multiple stages and dependencies.
As a Maintenance Associate, you can use this view to adjust the dates of your tasks and ensure you complete cards in sequence, without overloading yourself with too many activities at once. This will help you prioritize your tasks and make sure you meet your targets.
The main purpose of Timeline view is to organize tasks and determine their order. It allows you to create a new timeline view, manage cards with timeline view, adjust card dates, and customize the view as needed.
KanBo also has a Gantt Chart view for teams who need to focus on card relations and their time dependencies.
But KanBo isn’t just about efficient time management. Its on-premises and cloud installations cater to the needs and preferences of large enterprises, providing a platform for teams, departments, and external stakeholders to collaborate and share resources.
With KanBo, you can streamline project management, foster collaboration, and solve complex problems. Its focus on preventative maintenance, reliability, equipment improvement, countermeasure activities, equipment repairs, production support, safety, and training makes it an ideal platform for the automotive industry.
In conclusion, KanBo is a work coordination platform designed for large enterprises that value efficient time management and collaboration. Its Timeline view feature is an indispensable tool for teams working on complex projects, allowing them to plan and manage their workloads with ease. As a Maintenance Associate in the automotive industry, KanBo can help you ensure your tasks are completed on time and within budget, while also providing a platform for collaboration and problem-solving.
In this section we will provide a practical guide on how to effectively use KanBo and Time Management in your day-to-day work as a Maintenance Associate in the Automotive Industry. We will go through a typical workweek, from Monday to Friday, and show you how to efficiently manage your tasks using KanBo’s Timeline view.
Monday:
Start your week by opening KanBo and navigating to your workspace. Review your tasks and prioritize the most urgent ones by dragging and dropping them on the Timeline view. Adjust the dates of your cards to ensure that you use your time effectively. Use KanBo’s Time Management features to set reminders and notifications to keep track of deadlines and to stay on top of your work.
Tuesday:
As new tasks come in, add them to KanBo and assign them to other team members if necessary. Use the Timeline view to manage your workload and avoid overloading yourself. Make sure to focus on completing high-priority tasks first, before moving on to less urgent tasks.
Wednesday:
Use KanBo to collaborate with team members by leaving comments or sharing documents related to a particular task. This will help streamline communication and avoid confusion. If you need assistance, don’t hesitate to reach out to your team members for help.
Thursday:
As tasks are completed, update their status on KanBo to keep track of progress. Use the Timeline view to ensure that dependencies are taken into account, so that you don’t fall behind on any critical tasks. Keep an eye on the Current Time Bar to ensure that timelines are aligned with the present day.
Friday:
End your week by reviewing your progress and assessing the effectiveness of your workflow. Analyze your usage of KanBo and determine any areas where you can improve. Always strive to optimize your time management skills to ensure maximum productivity and efficiency.
In conclusion, by using KanBo and Time Management, you can effectively manage your tasks and stay on top of your workload as a Maintenance Associate in the Automotive Industry. Remember to prioritize your tasks, stay organized, and collaborate effectively with team members to ensure a successful workweek.
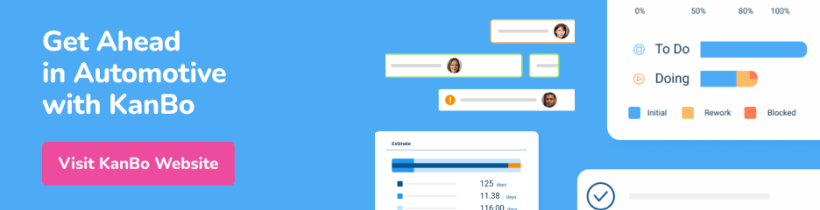
While KanBo is often recognized for its ability to optimize work management and help individuals and teams manage their time better, there is so much more to this powerful platform than simply time management. In addition to improving time management, KanBo is designed to help companies create agile organizations through improved communication, collaboration, and knowledge management. KanBo is much more than just a task management tool – it is designed to help individuals and teams work together more effectively and efficiently to achieve their goals.
One of the key benefits of using KanBo is its ability to facilitate communication and collaboration among team members and external stakeholders. Through its integration with popular communication tools like Microsoft Teams, KanBo enables teams to work together in real-time, no matter where they are located. Additionally, KanBo provides a central location for storing and sharing knowledge, allowing team members to quickly find the information they need to get their work done.
KanBo also provides a range of powerful productivity features that help individuals and teams work smarter, not harder. For example, the platform includes advanced analytics and reporting tools that enable managers to track progress, identify roadblocks, and make more informed decisions about how to allocate resources. It also includes a range of visualizations and tools to help individuals manage their workload more effectively, such as kanban boards, Gantt charts, and personal dashboards.
In short, while KanBo is undoubtedly one of the best tools available for time management, it is so much more than that. It is a powerful platform that is designed to bring teams together, improve communication and collaboration, and help organizations become more agile and productive. So if you’re looking for a tool that can help you take your team’s performance to the next level, then KanBo might just be the solution you’ve been looking for.
Q&A
Q: What is KanBo and how can it benefit large enterprises in the automotive industry?
A: KanBo is a work coordination platform designed for large enterprises that value efficient time management and collaboration. It can benefit the automotive industry by helping teams streamline project management, foster collaboration, and solve complex problems related to preventative maintenance, reliability, equipment improvement, countermeasure activities, equipment repairs, production support, safety, and training.
Q: How does Timeline view work in KanBo and what is its main purpose?
A: Timeline view in KanBo allows teams to visualize a project’s progress and dependencies in a single view, making it easier for them to plan and manage their workloads. Its main purpose is to organize tasks and determine their order. It allows users to customize the view as needed, create a new timeline view, adjust card dates and manage cards with timeline view, thereby providing an indispensable tool for ensuring projects are completed on time and within budget.
Q: What can Maintenance Associates in the automotive industry do with KanBo’s Timeline view feature?
A: Maintenance Associates can use KanBo’s Timeline view to adjust the dates of their tasks and ensure they complete cards in sequence, without overloading themselves with too many activities at once. They can use the feature to prioritize their tasks and make sure they meet their targets, while also collaborating and communicating effectively with team members to ensure a successful workflow.
Now let’s take a look at some use cases of KanBo’s Timeline view in the automotive industry. One of the key areas where this feature can be especially useful is equipment improvement projects. These projects involve making modifications to existing equipment to optimize their performance, reduce downtime, and prevent breakdowns. By using the Timeline view to schedule these tasks, teams can ensure that they don’t disrupt production schedules and complete the work on time.
Another area where Timeline view can be particularly useful is in countermeasure activities. These activities involve identifying and addressing potential problems before they can negatively impact production. By using this view to plan and manage these tasks, teams can minimize the risk of downtime, reduce costs, and improve overall equipment reliability.
Equipment repairs are also a critical part of automotive maintenance, and KanBo’s Timeline view can be used to schedule and manage these tasks more efficiently. By visualizing all the repair tasks on a single timeline and tracking progress, teams can ensure that repairs are completed quickly and effectively, minimizing downtime and maximizing production efficiency.
Production support tasks, such as setting up new lines, modifying existing lines, or integrating new equipment into existing lines, can also benefit from KanBo’s Timeline view. By visualizing all the tasks involved in these activities, teams can coordinate their efforts more effectively, minimizing the risk of delays and ensuring that all activities are completed on time.
In addition, KanBo’s Timeline view can be used to manage safety tasks and training activities in the automotive industry. For example, by scheduling safety inspections and training sessions on a timeline, teams can ensure that these tasks are completed regularly and that everyone is up to date on the latest safety protocols.
Finally, KanBo’s Timeline view is designed to be simple and user-friendly, making it easy for even the most novice users to use and understand. In fact, users with Microsoft Office skills will find it easy to work with KanBo’s Timeline view since it uses similar interface elements, such as drag and drop functionality, copy and paste, and time scales based on days, weeks, months, etc.
In conclusion, KanBo’s Timeline view is an essential tool for teams working in the automotive industry. It helps them better manage their tasks, improve productivity, and reduce downtime. By using this view to schedule and track tasks, teams can ensure that they complete their projects on time and within budget, making their operations more efficient and profitable.
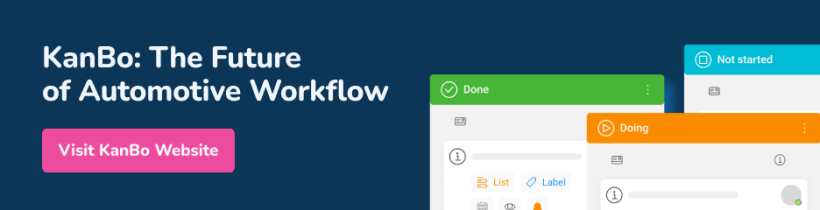