Work coordination platform
Designed for the automotive industry
As a leader in innovation, you understand the importance of staying ahead of the curve in the fast-moving automotive 4.0 world. KanBo provides you with the tools to do just that by facilitating smart factory operations, streamlining project management, fostering collaboration and solving complex problems.
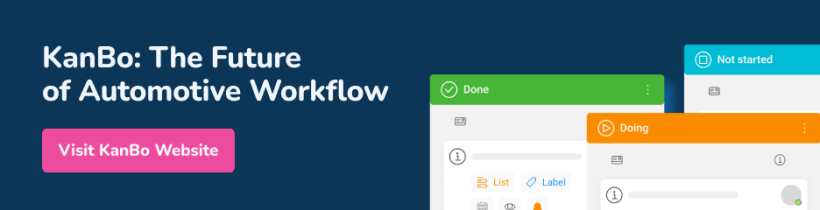
Efficient Time Management Tips for Component Supply and Procurement Specialists
KanBo – Work Coordination Platform Designed for Large Enterprises
Large enterprises are often bogged down by inefficient work processes, slow decision-making, and poor collaboration between teams. In such a scenario, a work coordination platform can be a game-changer. KanBo is one such platform that provides powerful features and capabilities to help large enterprises streamline their work processes, foster better communication, and improve collaboration between teams.
One of the key features of KanBo is Timeline View. This feature provides a visual representation of all the tasks and activities that need to be completed over a specific period. This view enables teams to see the progress of a project, the deadlines, and the dependencies in a single view. It makes it easier for teams to plan and manage their work, especially for complex projects with multiple stages and dependencies.
With the Timeline view, teams can adjust the dates of their projects in a fast and easy way. They can complete cards in sequence, avoiding overloading themselves with too many activities at once. This view also enables teams to control their workload and learn to prioritize their tasks better.
The main purpose of the Timeline view is to organize the tasks and activities that need to be done by determining the order of activities. Teams can create new Timeline views, manage cards, adjust card dates, and customize the Timeline view according to their specific needs.
KanBo also provides a Gantt Chart view that helps teams focus on card relations and their time dependencies if they want to delve into more complex work processes.
In the automotive industry, where time management is crucial to meet the demand of customers and keep up with the industry’s fast-moving nature, KanBo’s Timeline view can be particularly beneficial. It helps teams stay on top of production schedules, inventory management, and supplier coordination. In addition, with KanBo’s ability to integrate with other systems, such as ERP or CRM, teams can seamlessly share information and collaborate effectively to achieve their goals.
In conclusion, KanBo is a work coordination platform designed to help large enterprises improve their work processes, collaborate effectively, and achieve their business goals. Its Timeline view provides a powerful tool for teams to manage their workload, prioritize their tasks, and stay on top of complex projects. In the automotive industry, where time management is essential, KanBo’s capabilities can help teams stay competitive and innovative.
Introduction:
As a Component Supply/Procurement Specialist in the automotive industry, you know how important it is to manage your time effectively while juggling multiple projects and tasks. In this guide, we will show you how to use KanBo’s Timeline view to plan and manage your workweek, from Monday to Friday.
Monday:
Start your day by opening KanBo Workspace and navigating to the Timeline view. Review your tasks for the week and make any necessary adjustments. Prioritize urgent tasks that need to be completed first and adjust their start and end dates accordingly.
Tuesday:
Focus on completing the tasks you scheduled for the day. As you work through each task, update its status in KanBo and mark it as complete. This will help you stay organized and on track. Continue to adjust your tasks’ start and end dates to ensure that you are staying on top of your workload.
Wednesday:
Take some time to review any new requests that have come in since the beginning of the week. Use KanBo to quickly assess the time and resources required to complete the task and add it to your Timeline view as needed.
Thursday:
Collaborate with your team or vendors via KanBo Spaces to discuss any upcoming procurement requirements or supplier management needs. Use KanBo Cards to track communication and progress on each topic, ensuring that everyone is on the same page.
Friday:
Take some time to reflect on the week and evaluate your performance. Use KanBo’s reporting features to gather data on completed tasks, deadlines met, and overall productivity. Use this information to identify areas for improvement and make any necessary changes to improve your workflow for the upcoming week.
Conclusion:
With KanBo’s Timeline view and time management tools, you can effectively plan and manage your work week as a Component Supply/Procurement Specialist in the automotive industry. By prioritizing tasks, collaborating with team members, and tracking progress, you can ensure that you meet deadlines and deliver high-quality work.
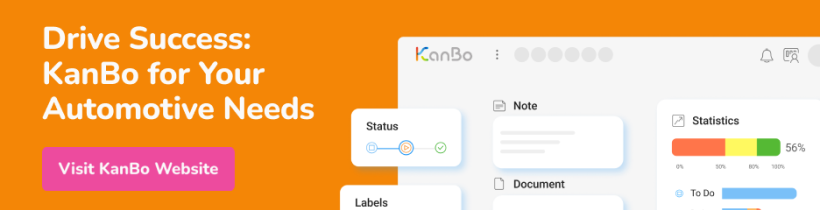
Yes, KanBo is much more than just a time management tool. While it is true that KanBo helps to optimize work management and maximize ROI on your on-premise SharePoint, Microsoft Office 365, Google Suite, AWS or Salesforce, it offers so much more than that.
KanBo is designed to bring all teams, departments, and external stakeholders in large enterprises together, with a focus on empowering purpose-driven organizations to optimize work management with full transparency and trust. KanBo’s philosophy is about simplifying work coordination so that people can focus on things only people can do.
For example, KanBo empowers company cultures based on transparency and trust. It supports different workstyles and hybrid methodologies across your organization to foster responsibility, autonomy, and mastery. By doing this, KanBo encourages people to take responsibility for things without fear of individual reprisal.
KanBo also creates powerful collaboration opportunities with colleagues who share their enthusiasm and drive, encouraging innovation along the way. This helps workers to reach their mission – as great as theirs is. KanBo’s less-is-more philosophy is the key to success, ensuring fast adoption in our information overloaded world.
Lastly, KanBo transforms technology into stuff that just works. It is an employee perspective on technology based on meaningful integrations that are in harmony with your choice of infrastructure and in peace with your IT department.
In summary, while KanBo offers great time management features, it’s so much more than that. It’s a tool that helps people simplify work, foster collaboration, and encourage innovation – all aimed at allowing workers to achieve their passions and meaningful work.
Q&A
Q1. What is the purpose of KanBo’s Timeline view?
A1. The main purpose of KanBo’s Timeline view is to provide a visual representation of tasks and activities that need to be completed over a specific period. It helps teams plan and manage their work, especially for complex projects with multiple stages and dependencies. The Timeline view enables teams to see the progress of a project, deadlines, and dependencies in a single view.
Q2. How can KanBo’s Timeline view be beneficial in the automotive industry?
A2. In the automotive industry, where time management is crucial to meet customer demand and keep up with the industry’s fast-moving nature, KanBo’s Timeline view can be extremely beneficial. It helps teams stay on top of production schedules, inventory management, and supplier coordination. With KanBo’s ability to integrate with other systems, teams can seamlessly share information and collaborate effectively to achieve their goals.
Q3. Can KanBo’s Timeline view be customized to suit specific needs?
A3. Yes, KanBo’s Timeline view is customizable and can be adjusted according to specific team needs. Teams can create new Timeline views, manage cards, adjust card dates, and customize the view to meet their specific needs. This customization not only improves collaboration and communication but also helps teams manage their workload more efficiently and prioritize their tasks better.
Let’s take a look at how the KanBo Timeline view can simplify component part ordering and expediting from Japan and domestic suppliers to support the non-current manufacturing of transmissions at the Honda and Remanufacturing plants as an example use case.
First, create a new Timeline view and add all the tasks related to the component part ordering and expediting process. These tasks can include placing orders with suppliers, tracking delivery dates, and ensuring on-time delivery to meet KOI objectives for customer backorders and inventory levels.
Use the Timeline view to adjust the dates of each task and see how they fit into the overall project timeline. This view makes it easy to prioritize tasks and ensure that critical activities are completed on schedule.
In addition, use the Timeline view to manage the transmission buildout activities with suppliers, Honda plants, and Japan to ensure that there is no impact on service part availability for Honda and Acura customers.
Furthermore, use the LET process support and backup at the Remanufacturing plant as a task in the Timeline view. This will ensure that the Remanufacturing plant has the necessary parts to support the production process.
Use Timeline view to manage the offsite component inventory storage and management at the Remanufacturing plant. This view makes it easy to keep track of inventory levels, order new parts, and ensure that there is no downtime due to parts shortages.
Finally, use the Timeline view to manage special projects as assigned to support the fiscal year business plan or department objectives. This can include tasks such as analyzing supplier performance data, negotiating supplier contracts, and optimizing inventory management practices.
By using the KanBo Timeline view, users can easily manage all tasks related to component part ordering and expediting. They can utilize their Microsoft Office skills to organize and prioritize their work, ensuring that critical tasks are completed on time while minimizing downtime due to parts shortages. With this simple yet powerful tool, teams in the automotive industry can streamline their work processes, foster better communication, and improve collaboration between teams, ultimately achieving their business goals.
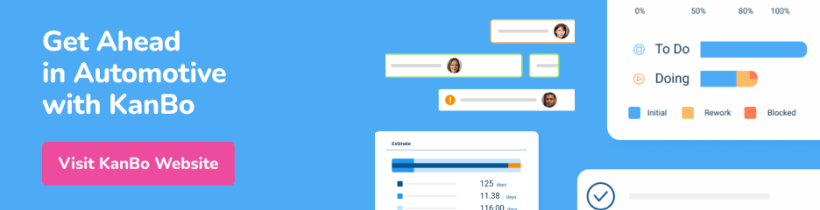