Work coordination platform
Designed for the automotive industry
As a leader in innovation, you understand the importance of staying ahead of the curve in the fast-moving automotive 4.0 world. KanBo provides you with the tools to do just that by facilitating smart factory operations, streamlining project management, fostering collaboration and solving complex problems.
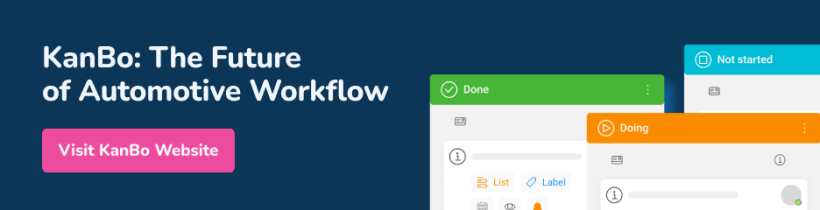
How KanBo Helps Automotive Enterprises with Time Management and New Model Parts Quality Group Lead Coordination
KanBo is a work coordination platform designed to meet the unique needs of large enterprises, especially those in the fast-moving automotive 4.0 world. With features that cater to the industry’s specific requirements, KanBo enhances time management and streamlines the project management process for teams within the sector.
One of the standout features of KanBo is its Calendar view. This view provides a clear, visual representation of tasks that are time-dependent, allowing for more efficient management of workload and identification of potential scheduling conflicts. With the ability to switch between day, week, and month views, teams can have a complete picture of their schedules to ensure that deadlines are met and projects are completed on time.
The KanBo platform also facilitates smart factory operations by providing tools for effective supply chain management. With the ability to integrate with existing systems and platforms, teams can easily manage suppliers and monitor progress throughout the new model part development process. KanBo also allows users to confirm the completion of the New Model Review process and full Part Maturation of all parts prior to mass production, reducing the risk of potential quality issues that could delay the production process.
KanBo’s focus on collaboration makes it an essential tool for large enterprises in the automotive industry. With the ability to connect all teams and external stakeholders, teams can work seamlessly together on project tasks. With KanBo, teams can coordinate and complete new model Part by Part Reviews and Trial Event parts inspection, and prepare New Model Evaluation documents to review with Parts Quality and Supplier Operations Department Management.
KanBo’s on-premises and cloud installations, licenses, and support options fit the needs of every type of business. Large enterprises can rest easy knowing that KanBo can scale to meet the needs of their growing businesses while ensuring that all user data is fully secure and accessible only to those with the proper permissions.
In conclusion, KanBo is a work coordination platform specifically designed for large enterprises in the fast-moving automotive 4.0 world. With its focus on time management, smart factory operations, collaboration, and data security, it is an essential tool for businesses that want to stay ahead of the curve in an ever-changing industry.
Introduction:
In the automotive industry, every week can bring new challenges and demands for quality and efficiency. As a New Model Parts Quality Group Lead, your role is crucial in ensuring that production runs smoothly and all products meet high standards. To help you manage your time and tasks effectively, you can use KanBo’s Calendar view. In this how-to guide, we will show you how to organize your week using KanBo and time management techniques. Let’s dive in!
Monday:
Start your week by reviewing your KanBo dashboard. Check for any urgent tasks or upcoming deadlines. Create a to-do list of tasks that need to be done this week, and assign priorities to each one. Use the Kanban board or List view to categorize tasks by status, such as “to do,” “in progress,” and “completed.” Set your work schedule for the week, and block off time for important tasks that need your full attention.
Tuesday:
Focus on tasks that require your immediate attention. Check in with team members and stakeholders to see if there are any updates or changes to the project. Use KanBo’s comments and @mention features to ask for clarification or provide feedback. Take breaks throughout the day to stay energized and avoid burnout.
Wednesday:
Midweek is a good time to review your progress and adjust your schedule if needed. Use KanBo’s Calendar view to see upcoming deadlines and schedule reminders. Update any incomplete tasks and reprioritize tasks for the rest of the week. Schedule a team meeting to discuss progress and address any issues.
Thursday:
As you approach the end of the week, focus on wrapping up any outstanding tasks and preparing for the next week. Use KanBo’s Reports feature to generate reports on team progress and project status. Schedule time for training or professional development to stay ahead of industry trends.
Friday:
Finish the week on a productive note by completing any remaining tasks and reviewing your accomplishments for the week. Use KanBo’s Activity view to track your progress and celebrate small wins. Reflect on what worked well and what challenges you faced during the week. Set goals for the following week, and schedule time to recharge and rest.
Conclusion:
Using KanBo’s Calendar view and time management techniques can help you stay organized, focused, and efficient as a New Model Parts Quality Group Lead in the automotive industry. By prioritizing tasks, scheduling reminders, and taking breaks, you can manage your workload effectively and achieve your goals. With KanBo, you can streamline your work processes, collaborate with team members, and stay ahead of the curve in the fast-moving automotive 4.0 world.
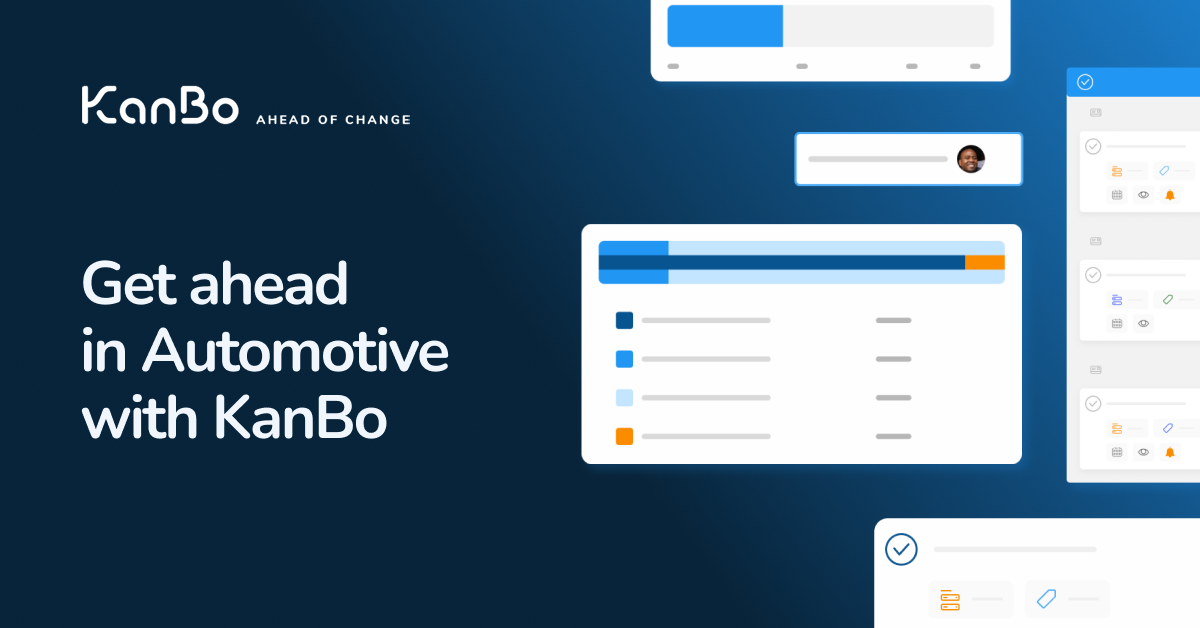
While KanBo is well-known for its features that allow for better time management, such as scheduling, card groupings, and reminders, it is much more than just a time management tool. KanBo is a comprehensive work coordination platform that streamlines communication, fosters collaboration, and promotes transparency and trust among team members.
One of the key features of KanBo is its ability to bring all teams and departments in an organization together in one place. By centralizing work and providing a single source of truth, KanBo eliminates silos and promotes cross-functional collaboration. This leads to increased productivity, faster decision-making, and a stronger sense of shared ownership and accountability.
KanBo also offers a variety of views that allow teams to visualize and manage work in ways that work best for them. From Kanban and list views to Gantt charts and timeline views, KanBo provides flexible and customizable tools that can cater to a range of workflows and methodologies.
Furthermore, KanBo’s integrated communication tools, such as comments, mentions, and activity streams, allow for real-time collaboration and feedback. Members can easily communicate about tasks and projects, share ideas, and stay up-to-date on changes and progress.
Finally, KanBo prioritizes transparency and trust in all aspects of its platform, from its user interface to its pricing model. With KanBo, users have full visibility and control over their data and can trust that it will remain secure and confidential. Additionally, KanBo offers a transparent and straightforward pricing structure that allows businesses to scale their use of the platform as needed.
In summary, KanBo is a comprehensive work coordination platform that offers much more than just time management tools. With its focus on collaboration, communication, transparency, and trust, KanBo empowers teams and organizations to work more efficiently and effectively towards their goals.
Q&A
Q1: What features specifically cater to the needs of large enterprises in the automotive industry?
A1: KanBo offers several features designed to meet the unique needs of large enterprises in the automotive industry, including the Calendar view, which provides a clear visual representation of time-dependent tasks. The platform also facilitates effective supply chain management and can integrate with existing systems and platforms to monitor progress throughout the new model part development process. Additionally, the platform’s collaboration tools connect all teams and external stakeholders, allowing teams to work together seamlessly on project tasks.
Q2: How can KanBo help with smart factory operations?
A2: KanBo provides tools for effective supply chain management to support smart factory operations. The platform allows teams to manage suppliers and monitor progress throughout the new model part development process. KanBo also allows users to confirm the completion of the New Model Review process, full Part Maturation of all parts prior to mass production, and prepare New Model Evaluation documents to review with Parts Quality and Supplier Operations Department Management. By streamlining these processes, KanBo reduces the risk of quality issues that could delay the production process.
Q3: How does KanBo ensure data security?
A3: KanBo’s on-premises and cloud installations, licenses, and support options fit the needs of every type of business. The platform ensures that all user data is fully secure and accessible only to those with the proper permissions. KanBo also offers various security measures, including two-factor authentication, automatic backups, and disaster recovery capabilities, to protect against data loss or unauthorized access.
Use Case: Lead supplier part tooling development throughout the new model cycle with KanBo
Managing OEM suppliers is a critical aspect of the automotive industry, especially during the development of new models. This process requires seamless communication and coordination between various teams, departments and external stakeholders. KanBo’s Work coordination platform provides a solution to this challenge.
Let’s take an example of a Lead supplier part tooling development throughout the new model cycle. This process involves multiple tasks, milestones, due dates, and dependencies. Using KanBo’s Calendar view, the teams involved can easily track progress and stay on top of deadlines. The teams can:
– Confirm the receipt of Quality Assurance Notice (QAN) documents from suppliers to evaluate results and implement countermeasures needed to achieve part approval.
– Coordinate and complete new model Part by Part Reviews and Trial Event parts inspection.
– Confirm Completion of the New Model Review process (NMR) and full Part Maturation of all parts prior to mass production
– Prepare New Model Evaluation documents to review with Parts Quality (PQ) and Supplier Operations Dept. (SOD) Management to address concern items and share countermeasure activities tasks in Automotive Industries.
The teams involved in this process can use the KanBo platform to store and share documents, track progress, and communicate with each other in real-time. The KanBo platform also integrates with Microsoft Office, allowing you to use your existing skills to manage your tasks.
Conclusion
KanBo’s Calendar view is a powerful tool that helps teams in the automotive industry manage their tasks and projects efficiently. With its visual representation of tasks, ability to track progress and manage timelines, KanBo simplifies complex processes. Teams can work together seamlessly, communicate in real-time, and access the necessary information they need to make informed decisions. The platform also offers flexibility, customization and scalability to fit the needs of any organization. Do give KanBo a try and see how it can transform your automotive business.
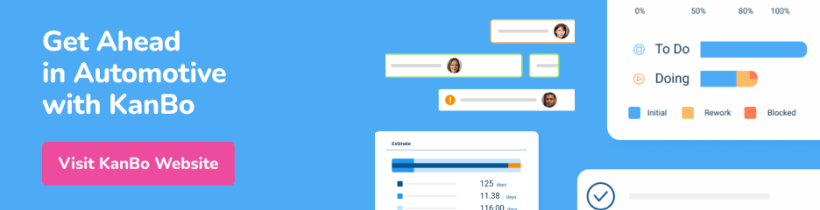