Work coordination platform
Designed for the automotive industry
As a leader in innovation, you understand the importance of staying ahead of the curve in the fast-moving automotive 4.0 world. KanBo provides you with the tools to do just that by facilitating smart factory operations, streamlining project management, fostering collaboration and solving complex problems.
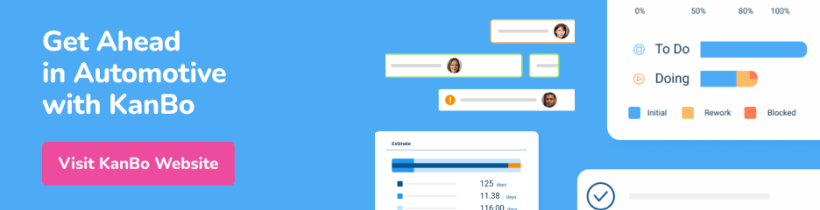
Maximizing Efficiency: Time Management Tips for Tool Room Machinists
In today’s rapidly evolving automotive industry, time management is a key factor that can make or break a business’s success. With a wide range of stakeholders, from multiple departments, teams, and even external partners, coordinating and managing everyone’s work can be a daunting task. This is why KanBo, a work coordination platform designed for large enterprises, is a game changer.
KanBo offers a range of tools that enable businesses to streamline project management and foster collaboration across teams, regardless of their locations. One of the platform’s standout features is scheduling cards. With scheduling cards, businesses can easily set start and due dates for tasks and visualize them with board views. The platform also provides personal reminders that are visible only to the individual user, allowing everyone to stay on top of their own workload.
Adding a date to a card is a simple process. Users can select the specific date and time from the mini calendar or pick an option under “card dates,” which provides more flexibility. Users can also edit or delete dates for a card easily.
Quick Actions are another powerful feature of KanBo. They allow users to set start or due dates faster and make changes or remove them without entering the card. These functions help users stay organized and focused on what’s important.
In the automotive industry, where time is always of the essence, KanBo’s time management features are crucial. With KanBo, businesses can improve their productivity, reduce downtime, and increase efficiency. This means that they can get their products to market faster and stay ahead of the competition.
In conclusion, KanBo is a work coordination platform designed for large enterprises that offers a range of features to streamline project management and foster collaboration across teams. Its scheduling cards and quick actions help users stay on top of their work and improve their time management. In the fast-paced world of the automotive industry, KanBo is a tool that can help businesses stay ahead of the curve.
Introduction:
Being a Tool Room Machinist in the automotive industry can be a challenging and demanding role that requires excellent time management skills. With the help of KanBo, you can effectively manage your tasks, prioritize deadlines and optimize your workweek. In this guide, we will walk you through how to use KanBo to plan and manage your workweek as a Tool Room Machinist in the automotive industry.
Monday:
Start your week by logging into KanBo and reviewing your task list. Prioritize tasks based on their importance and plan your day accordingly. Use KanBo’s scheduling feature to set start and due dates for tasks, and use personal reminders to keep you on track. Throughout the day, update your task status and communicate with team members, using KanBo’s collaboration features.
Tuesday:
Utilize KanBo’s dashboards and reports to monitor your project progress and identify areas that require attention. Use KanBo’s resource management feature to allocate resources effectively and ensure that projects stay on track. Stay on top of deadlines by using KanBo’s notifications and activity streams to keep track of progress and updates.
Wednesday:
Use KanBo’s visualization tools to gain a deeper understanding of project flow and identify potential bottlenecks. Use the Kanban and Gantt chart views to visualize work and identify areas that require attention. Leverage KanBo’s collaboration features to communicate with team members and address issues quickly.
Thursday:
Use KanBo’s document management feature to keep track of project documents, contracts, and other essential files. Use KanBo’s document versioning feature to ensure that all team members are working from the latest version of critical documents. Use KanBo’s search feature to quickly find and access necessary documents.
Friday:
Review your progress for the week, and evaluate your performance against your targets. Use KanBo’s analytics and reporting features to identify areas for improvement and make adjustments to your workflow for optimal performance. Use KanBo’s follow feature to stay informed of changes and updates to critical tasks and projects.
Conclusion:
By leveraging KanBo’s time management and collaboration features, Tool Room Machinists in the automotive industry can optimize their workflow, stay informed, and deliver high-quality results. With the help of KanBo, you can effectively manage your workweek, improve your productivity, and achieve your goals.
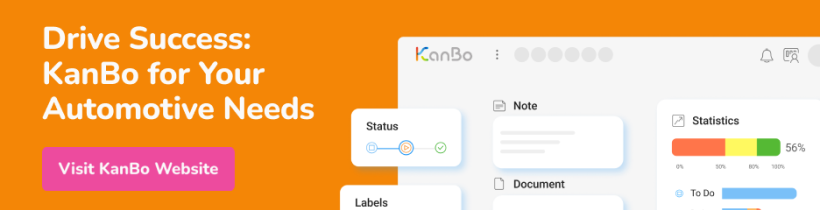
KanBo is much more than just a tool for time management. While it certainly helps you manage your time more efficiently, it is ultimately designed to help you optimize work management. KanBo achieves this by creating a work coordination platform that encourages full transparency and trust, empowering people to work the way they were meant to. KanBo supports different workstyles and hybrid methodologies, allowing individuals to take responsibility and make autonomous decisions.
KanBo enables company cultures that are built on transparency and trust, promoting a sense of ownership and accountability among team members. Instead of wasting time attending low-value meetings and dealing with micromanagement and politics, KanBo allows individuals to clarify responsibilities and collaborate with ease, freeing them up to focus on more meaningful work.
KanBo’s less is more philosophy is reflected in its Art of Moderation approach to features. Its objective is to help users realize the most important aspects of work, while filtering out the unnecessary and simplifying work management.
KanBo’s history bears testament to its continuous evolution and development as an enterprise class capable version for both on-premises and cloud installations and licenses. From its introduction as a minimal viable product based on SharePoint 2010, KanBo has since won awards for Best Social Strategy and Best Office 365, and has expanded to include features such as Board Analytics, Gantt Chart, Sub-Cards, Email to KanBo, and List/Status roles, among others.
The bottom line is that KanBo supports individuals and organizations to achieve their goals by helping them work effortlessly and harmoniously. It transcends the conventional tool for time management and emphasizes the significance of full transparency, trust, and collaboration in optimizing work management.
Q&A
1. Question: What are some of the standout features of KanBo that make it a valuable tool for Tool Room Machinists in the automotive industry?
Answer: KanBo offers a range of features that can help Tool Room Machinists in the automotive industry streamline their workflow and manage their time more effectively. Some of the standout features of KanBo include scheduling cards, quick actions, dashboards and reports, resource management, document management, and analytics and reporting. These features can help Tool Room Machinists prioritize tasks, stay on top of deadlines, visualize their work, communicate with team members, and monitor progress.
2. Question: How can KanBo help Tool Room Machinists in the automotive industry improve their productivity?
Answer: KanBo offers several features that can help Tool Room Machinists in the automotive industry improve their productivity. By using KanBo’s scheduling feature, Tool Room Machinists can prioritize tasks and set start and due dates, ensuring that they manage their workload effectively. KanBo’s dashboards and reports can also help Tool Room Machinists monitor progress and identify areas that require attention. Finally, KanBo’s quick actions and collaboration features can help Tool Room Machinists stay organized and communicate with team members efficiently, thereby optimizing their productivity.
3. Question: How can Tool Room Machinists use KanBo’s analytics and reporting features to improve their workflow?
Answer: KanBo’s analytics and reporting features can provide Tool Room Machinists with valuable insights that can help them optimize their workflow. By analyzing data on task completion rates, resource allocation, and other metrics, Tool Room Machinists can identify areas for improvement and make adjustments to their workflow as needed. Additionally, KanBo’s reporting features can help Tool Room Machinists communicate progress and performance to stakeholders, ensuring that everyone is aware of project status and goals.
Use Case: Regrinding and Presetting of Cutting Tools
One of the many tasks in the automotive industry is the regrinding and presetting of cutting tools. This involves resetting the cutting edges of drill bits, end mills, and other cutting tools to their original sharpness, as they become dull after repeated use. Teams performing this task need to have good coordination, time management, and attention to detail to ensure that the tools are returned to their original cutting efficiency, without any delays.
KanBo delivers a simple solution to this complex task with its scheduling cards. Team leaders can assign tasks to team members and set due dates for them. The team members can then view these tasks on their KanBo board and execute them accordingly, based on priority. For instance, the team leader can assign a large number of drill bits to one team member with the due date set for the end of the day, while another team member can be assigned to regrind a single end mill with a due date for the following day.
Users can also use their Microsoft Office skills to make the most of scheduling cards. For example, they can import data from Excel spreadsheets into KanBo to populate cards with tasks and due dates. This reduces data entry errors and speeds up the process of creating new cards.
When using KanBo, adding dates to cards is a simple process. You can select a specific date and time from the mini calendar or pick an option under “card dates” for more flexibility. If you want to edit or delete a date for a card at any time, it can be done in just a few clicks.
Quick Actions in KanBo make the whole process even faster, allowing users to set start or due dates without even entering the card. This enables team members to stay focused on the task at hand, and make changes or remove deadlines in a jiffy.
In the case of cutting tool regrinding and presetting, KanBo’s scheduling cards and Quick Actions enable teams to work efficiently and avoid delays. With all tasks assigned, due dates set, and reminders in place, your team can ensure that cutting tools are returned to their optimum sharpness, resulting in better quality of work, higher productivity, and more satisfied customers.
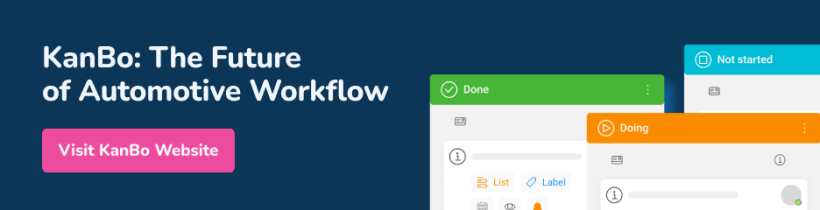